Components
Various raw materials are used in preparing ceramic bodies and, depending on the behaviour of these materials on dispersion in water, they are divided into plastic or fat materials and non-plastic or lean materials. Fat materials are the ceramic raw materials par excellence, consisting basically of clays and kaolins. Lean materials are substances that are incorporated into the body formulation with a view to reducing plasticity, controlling product quality, or adding specific properties. The most frequent lean materials are silica sands, alkaline feldspars, calcium carbonates, talcs, zirconium silicates, and colorants.
Plastic or fat materials
Clay. A universal component used in preparing ceramics owing to its extraordinary ease of transformation through mouldingand hardening processes. Although there are numerous classifications, the most common classification in the manufacture of ceramic coverings is based on the colour of the body-red or white-. Red-body clays are characterised by their high iron content, low melting temperature, and moderate plasticity, whereas white-body clays are more plastic and have no colouring oxides.
Kaolín. Very pure white clay used in preparing porcelain, as it keeps its colour during the firing process. It is more difficult to press and requires a higher firing temperature.
Non-plastic or lean materials
Silica sand. Ingredient that reduces shrinkage of the pieces in the kiln and increases their porosity once they have been fired. Excess silica sand reduces the mechanical strength and raises the coefficient of expansion of the end product.
Alkaline feldspar. Ingredient that acts as a fluxing element at high temperature, facilitating the reactivity of the mixture by lowering the firing temperature needed to reach a given apparent porosity.
Calcium carbonate. Ingredient that provides high strength before reaching the melting temperature by reducing the risk of liquefaction. It also increases the porosity and water absorptionof the end product, while contributing to greater dimensional stability.
Talc. Ingredient that increases the expansion coefficient and decreases the moisture expansion of the fired product in earthenware tile manufacture, while it increases fusibility in white-body stoneware floor tile compositions.
Colorants. Pigments obtained by calcining natural oxides, used for colouring the ceramic body.
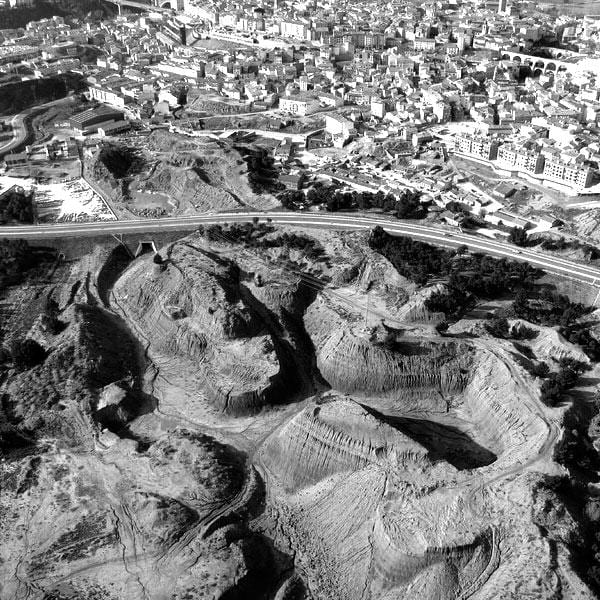
Aerial view of clay quarries in Teruel, Spain.
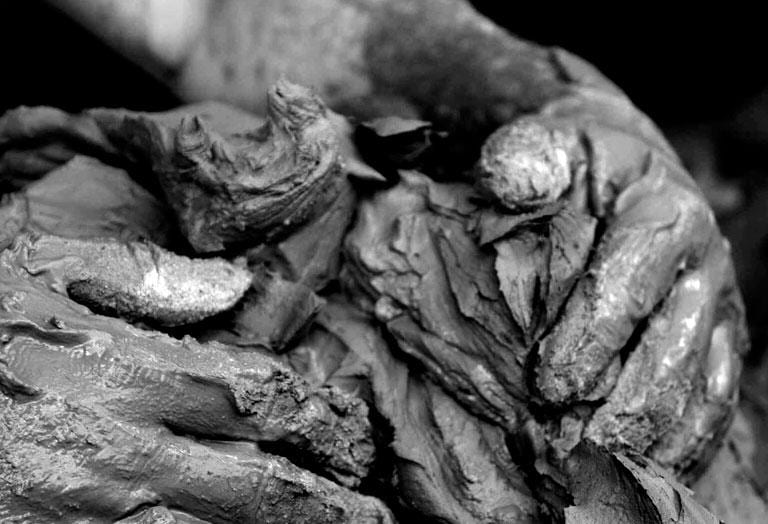
Manual wet-mixing process of the clay body.