Componentes
Para la elaboración de las pastas cerámicas se utilizan diversas materias primas y en función del comportamiento que ofrezcan al ser dispersadas en agua, se clasifican en plásticas o grasas y no plásticas o desengrasantes. Las grasas son las materias primas por excelencia y están compuestas fundamentalmente por arcillas y caolines. Las desengrasantes son substancias que se incorporan a la formulación de la pasta con el fin de disminuir la plasticidad, controlar la calidad del producto o añadirle propiedades específicas, siendo las más frecuentes: arenas silíceas, feldespatos alcalinos, carbonatos cálcicos, talcos, silicatos de circonio o colorantes.
Plásticos o grasos
Arcilla. Componente universal utilizado en la elaboración de objetos cerámicos debido a su extraordinaria facilidad de transformación a través de los procesos de modelado y endurecimiento. Aunque existen múltiples clasificaciones, la más común en la fabricación de los revestimientos cerámicos se realiza en función del color de la pasta -roja o blanca-; las arcillas de pasta roja se caracterizan por su alto contenido en hierro, su baja temperatura de fusión y su moderada plasticidad, y las de pasta blanca por ser más grasas y estar libres de óxidos colorantes.
Caolín. Arcilla blanca muy pura utilizada en la elaboración de porcelana, ya que conserva su tonalidad durante el proceso de cocción. Es más difícil de prensar y requiere de una temperatura de cocción más elevada.
No plásticos o desengrasantes
Arena silícea. Ingrediente que reduce la contracción de las piezas en el interior del horno y aumenta su porosidad una vez cocidas. Su presencia en exceso disminuye la resistencia mecánica e incrementa el coeficiente de dilatación del producto final.
Feldespato alcalino. Ingrediente que actúa como elemento fundente a alta temperatura, facilitando la reactividad de la mezcla al reducir la temperatura de cocción necesaria para alcanzar una determinada porosidad abierta.
Carbonato cálcico. Ingrediente que confiere alta resistencia antes de alcanzar la temperatura de fusión al reducir el riesgo de licuefacción. También aumenta la porosidad de la pieza final y su absorción de agua, contribuyendo al incremento de la estabilidad dimensional.
Talco. Ingrediente que incrementa el coeficiente de dilatación y disminuye la expansión por humedad del producto cocido en la fabricación de los azulejos, y aumenta la fundencia en las composiciones de gres de pasta blanca usadas para pavimentos.
Colorantes. Pigmentos obtenidos por calcinación de óxidos naturales que tienen por finalidad colorear la pasta cerámica.
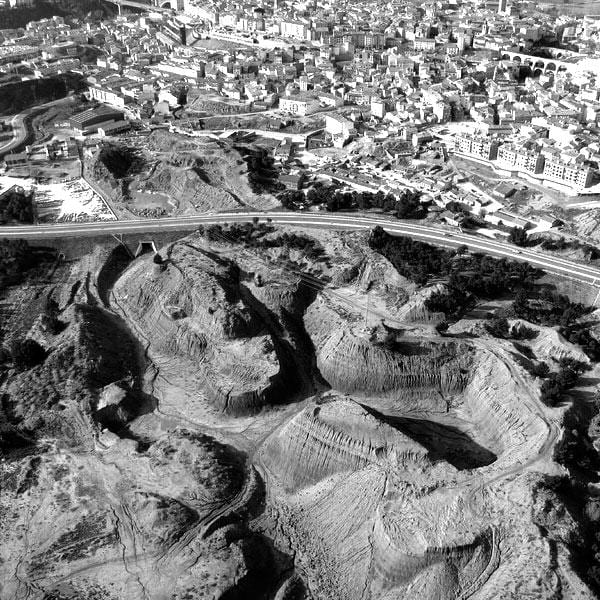
Vista aérea de canteras de extracción de arcilla en Teruel, España.
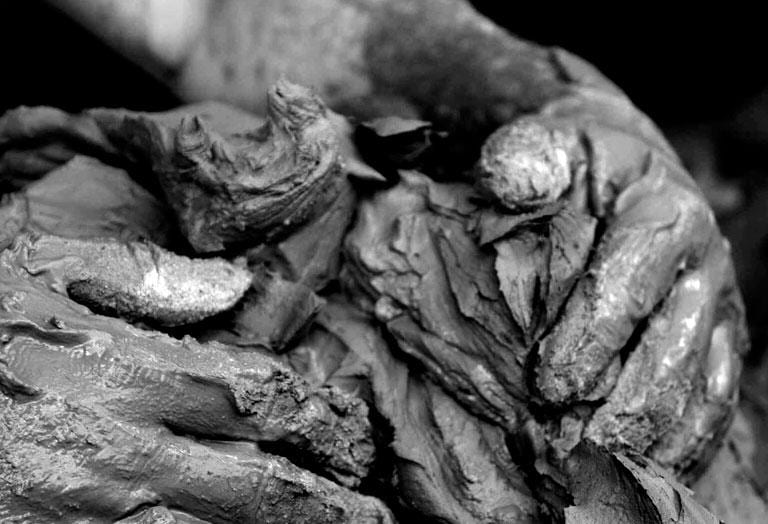
Proceso de amasado manual de la pasta de arcilla.